Safety relay modules and safety controllers are devices used in the safety-related part of control systems to perform control so that the machine operation is permitted only when safety is confirmed.
Specifically, it checks signals from inputs such as emergency stop switches and interlock switches, determines that it is safe, and controls contactors and other devices connected to outputs based on the results of that determination. In other words, the safety relay module and safety controller play a central role as the logic unit in the safety-related part of the control system (Figure 1).
- 首页
- Safety relay module / safety controller
解决方案
IDEC的无铜化产品
IDEC的无铜化产品
降本增效
小型控制设备
小型控制设备
LED 照明
LED 照明
可编程控制器
可编程控制器
编程软件、机种选型系统
编程软件、机种选型系统
长使用寿命的控制设备
长使用寿命的控制设备
降本增效
减碳排放
PID控制/热力工程技术
PID控制/热力工程技术
实现高效供电
实现高效供电
LED照明单元
LED照明单元
12VDC型PLC
12VDC型PLC
太阳能发电系统解决方案
太阳能发电系统解决方案
减碳排放
安全及其未来
协同安全
协同安全
Safety 2.0
Safety 2.0
第3代紧急停止开关
第3代紧急停止开关
机械安全
机械安全
功能安全
功能安全
安全咨询
安全咨询
追踪系统
追踪系统
安全及其未来
降低停机时间
长使用寿命且耐久性卓越的设备
长使用寿命且耐久性卓越的设备
远程监视、控制
远程监视、控制
预测性·预防性维护
预测性·预防性维护
更换简单
更换简单
避免因事故引发停机时间
避免因事故引发停机时间
降低停机时间
工业物联网优化作业
一键检查
一键检查
扫描产品
扫描产品
使用智能设备
使用智能设备
利用传感器
利用传感器
工业物联网优化作业
防爆
Remote Monitoring
Remote Monitoring
机械安全
机械安全
减少维修
减少维修
Traceability
Traceability
Expertise Support
Expertise Support
防爆
解决劳动力短缺
防爆结构摄像头
防爆结构摄像头
运用工业机器人
运用工业机器人
远程监视、控制
远程监视、控制
预防性维护
预防性维护
预测性维护
预测性维护
自动化
自动化
解决劳动力短缺
- IDEC的无铜化产品
- IDEC的无铜化产品
- 降本增效
- 小型控制设备
- 小型控制设备
- LED 照明
- LED 照明
- 可编程控制器
- 可编程控制器
- 编程软件、机种选型系统
- 编程软件、机种选型系统
- 长使用寿命的控制设备
- 长使用寿命的控制设备
- 降本增效
- 减碳排放
- PID控制/热力工程技术
- PID控制/热力工程技术
- 实现高效供电
- 实现高效供电
- LED照明单元
- LED照明单元
- 12VDC型PLC
- 12VDC型PLC
- 太阳能发电系统解决方案
- 太阳能发电系统解决方案
- 减碳排放
- 安全及其未来
- 协同安全
- 协同安全
- Safety 2.0
- Safety 2.0
- 第3代紧急停止开关
- 第3代紧急停止开关
- 机械安全
- 机械安全
- 功能安全
- 功能安全
- 安全咨询
- 安全咨询
- 追踪系统
- 追踪系统
- 安全及其未来
- 降低停机时间
- 长使用寿命且耐久性卓越的设备
- 长使用寿命且耐久性卓越的设备
- 远程监视、控制
- 远程监视、控制
- 预测性·预防性维护
- 预测性·预防性维护
- 更换简单
- 更换简单
- 避免因事故引发停机时间
- 避免因事故引发停机时间
- 降低停机时间
- 工业物联网优化作业
- 一键检查
- 一键检查
- 扫描产品
- 扫描产品
- 使用智能设备
- 使用智能设备
- 利用传感器
- 利用传感器
- 工业物联网优化作业
- 防爆
- Remote Monitoring
- Remote Monitoring
- 机械安全
- 机械安全
- 减少维修
- 减少维修
- Traceability
- Traceability
- Expertise Support
- Expertise Support
- 防爆
- 解决劳动力短缺
- 防爆结构摄像头
- 防爆结构摄像头
- 运用工业机器人
- 运用工业机器人
- 远程监视、控制
- 远程监视、控制
- 预防性维护
- 预防性维护
- 预测性维护
- 预测性维护
- 自动化
- 自动化
- 解决劳动力短缺
Safety relay module / safety controller | 中国
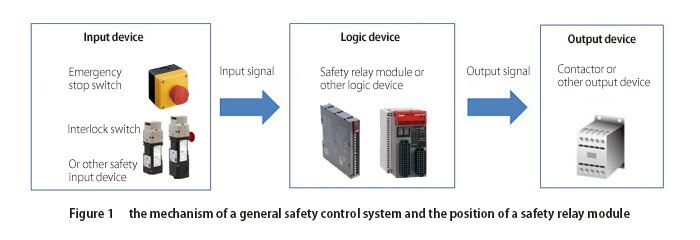
Safety Relay Modules
A typical safety relay module contains several force guided relays and electronic components in an enclosure. It is also designed to be installed inside the control panel.(e.g. on a DIN rail)
Function of Safety Relay Modules / Safety Controllers in the Safety-related Part of a Control System
To start, the overall function of the safety-related part of the control system will be explained. As an example, we use a system with a safety function where a contactor opens and closes the load (motor) circuit in response to operation of an emergency stop switch (Figure 2). If the emergency stop switch is pressed while the motor is running, the motor is stopped immediately.
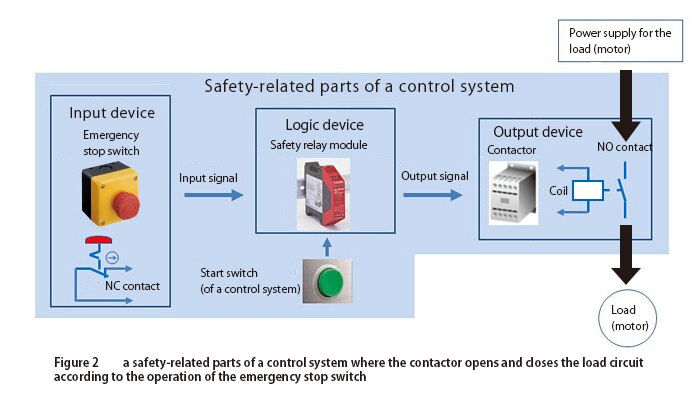
Emergency stop switches use NC (normally closed) contacts, which are normally closed (turned on) and output a signal (safety signal) that indicates a safe state. On the other hand, if some problem occurs and an emergency stop switch is used (pressed), the NC contact opens (turns off), and the safety signal is no longer output.
The safety relay module / safety controller outputs a signal to the contactor that permits the motor to run when the safety signal from the emergency stop switch has been input and the start (activation) switch of the control system has been pressed. When the contactor contacts are closed (turned on) and power is supplied from the power supply, the motor will start running. Note that the contactor contacts are NO (normally open) and are open (off) when there is no signal from the safety relay module.
In this type of safety control system, if the emergency stop switch is pressed while the motor is running, the safety signal is no longer input to the safety relay module, and the safety relay module stops outputting the signal to the contactor (the signal that allows the motor to run). In response, the NO contact of the contactor shall also open (turn off), and the motor shall stop.
Furthermore, when the emergency stop switch is pressed, even if the start switch is pressed, the safety relay module shall not output a signal (to allow the motor to run) to the contactor, and so the motor shall not run. To restart the motor, the emergency stop switch shall be reset (released from the activated state), and then the start switch shall be pressed separately.
The safety relay module / safety controller outputs a signal to the contactor that permits the motor to run when the safety signal from the emergency stop switch has been input and the start (activation) switch of the control system has been pressed. When the contactor contacts are closed (turned on) and power is supplied from the power supply, the motor will start running. Note that the contactor contacts are NO (normally open) and are open (off) when there is no signal from the safety relay module.
In this type of safety control system, if the emergency stop switch is pressed while the motor is running, the safety signal is no longer input to the safety relay module, and the safety relay module stops outputting the signal to the contactor (the signal that allows the motor to run). In response, the NO contact of the contactor shall also open (turn off), and the motor shall stop.
Furthermore, when the emergency stop switch is pressed, even if the start switch is pressed, the safety relay module shall not output a signal (to allow the motor to run) to the contactor, and so the motor shall not run. To restart the motor, the emergency stop switch shall be reset (released from the activated state), and then the start switch shall be pressed separately.
Safety Controllers
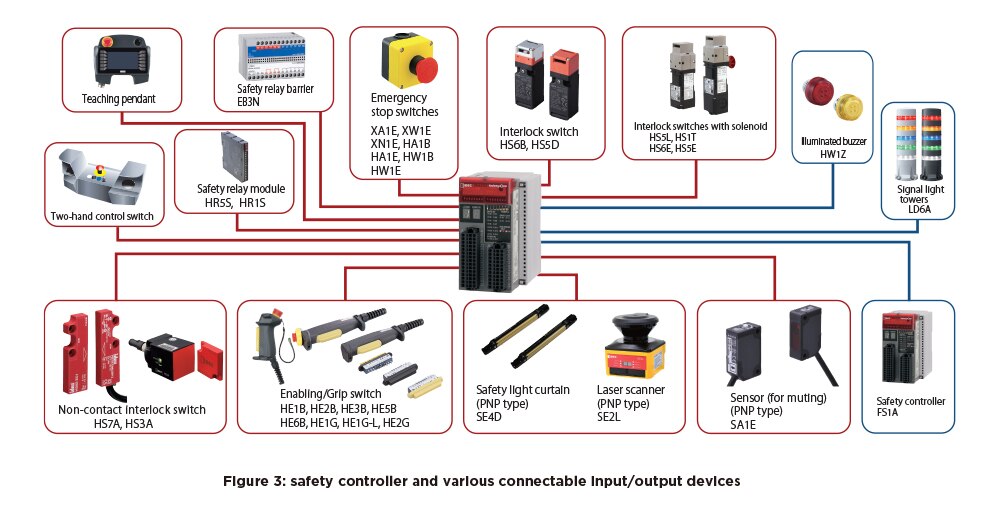
The safety controller is a safety device that, like the safety relay module, serves as the logic unit in the safety-related part of a control system.
As machines become more sophisticated and various safety devices are introduced, the safety-related part of control systems will continue to grow in complexity. The safety controller can be said to be a device that combines high safety performance with ease of use because the CPU functions can be used to easily set up the logic processing and combinations of various safety devices needed to ensure machine safety (Figure 3).
As machines become more sophisticated and various safety devices are introduced, the safety-related part of control systems will continue to grow in complexity. The safety controller can be said to be a device that combines high safety performance with ease of use because the CPU functions can be used to easily set up the logic processing and combinations of various safety devices needed to ensure machine safety (Figure 3).