We are pursuing four basic strategies under the current medium-term management plan for FY2023–FY2025: promote growth strategies, improve profitability, enhance the business foundation, and enhance ESG initiatives. Specific themes linked with our materiarities have been defined for each strategy, and we are taking action on them to realize our slogan of “PASSION FOR YOUR SUCCESS.” Leveraging the control technologies we have cultivated over the years, we are striving to achieve advances in our core fields, including answering needs for automation, unmanned operation, and labor-saving, and increasing safety, ANSHIN, and well-being. In doing so, we seek to advance our new concept of HMI-X, help solve societal challenges, and achieve sustainable growth and customer success. As we achieved the medium-term management plan’s original numerical targets in its first year, we announced an updated plan in May 2023. We are pursuing radical reforms under the current plan to realize an operating income margin of 20% or higher in the medium to long-term, with the aim of achieving greater profitability. We are also strengthening our business foundation to attain sustainable growth worldwide. These efforts include reducing our environmental impact toward the achievement of carbon neutrality, and improving employee engagement through increased investment in human capital, implementation of workstyle reforms, and other measures.
Growth Strategy: Actions for advancing HMI-X 1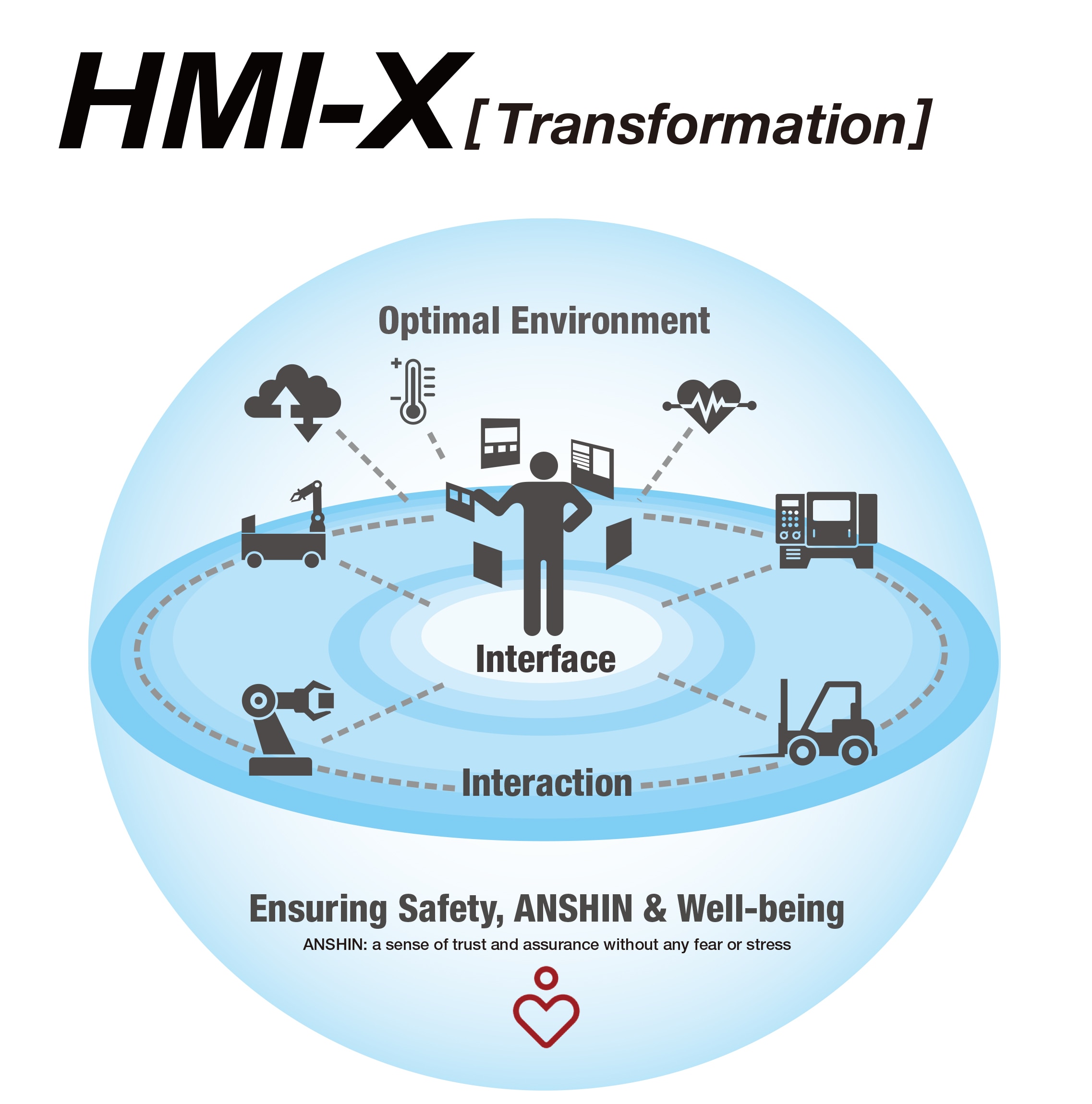
Expand new markets through collaborations
As part of the medium-term management plan’s growth strategy, we will seek to expand new product development and sales networks through collaborations with leading companies in diverse industries. We will also work to expand new markets by developing products offering new functions, with the aim of realizing the new concept of HMI-X [Transformation].
IDEC ALPS Technologies Co., Ltd., established as a joint venture with ALPS ALPINE CO., LTD. in September 2021, carries out product development aimed at providing new forms of value in HMI that contribute greater safety and ANSHIN to society. The joint venture launched the “1A1M series” of Multi-use mmWave (millimeter wave) radar sensors in May 2023. This is the first product developed through collaboration among IDEC and ALPS ALPINE sites in Japan and abroad.
This product is also an innovation that combines the strengths in HMI and sensing technology of two partners with different cultures and way of thinking.
Other products are now being developed. Once marketed, the full product portfolio, including the 1A1M series, is planned to grow into a JPY 1 billion business over a three-year period.
●Development leveraging each partner’s strengthsThe recently launched Multi-use mmWave radar sensors detect objects using high-frequency radar (in this case, 60GHz), which enables presence detection and distance determination for objects up to 10 meters away. This type of radar consumes little power and operates in a wide range of environmental conditions, including steam, dust, rain, snow and low sunlight.Therefore it can be used instead of ultrasonic sensors, both outdoors and in Factory Automation.
Until now, mmWave radar technology was primarily used in automobiles, and consequently very few products incorporating these sensors had been developed for use in industrial equipment. We were able to create a unique, highly competitive product optimally matched to the needs of industrial customers by leveraging our HMI technologies and expertise along with the technologies that ALPS ALPINE cultivated in consumer and automotive applications, and by steadily building up our know-how through joint testing with customers.
In addition to the launched versions, further models with different lens design for more specific applications are planned to be offered. This series supports a broad range of industrial needs, including not only factory automation, but also for specialized vehicles, parking lots, train stations, and infrastructure.
Presence detection
-Vehicle detection in parking lots (an algorithm for distinguishing between vehicles and humans will be added)
-Identification of light-absorbing materials (rubber, dark-colored workpieces, etc.)
Distance determination
-Determination of width of vehicles entering carwashes
-Determination of fluid level in tanks from the outside via a viewport
Growth Strategy: Actions for advancing HMI-X 2
Provide diverse applications for realizing safety, ANSHIN, and well-being
As part of our efforts to fulfill our Purpose—to create the optimum environment for humans and machines, and to achieve safety, ANSHIN, and well-being for people around the world, we develop and supply a broad range of products and systems designed to solve the needs of customers in not only the factory automation industry but also many other sectors. The main focuses of our medium-term management plan are HMI and safety, and there is growing demand for collaborative safety / Safety2.0, whereby humans and machines collaborate for greater safety.
Accordingly, we are expanding our diverse lineup of applications that can improve worker well-being by enabling the creation of environments where people can work with ANSHIN.
Case1: Emergency-stop assist system
We hold a 70% share of Japan’s market in emergency-stop switches, offering international standard-compliant products that incorporate our proprietary safety technology. Once activated, emergency-stop switches reliably stop the machines they control.
However, they need to be pushed to operate, and this can be an issue when they are installed on mobile robots such as automatic guided vehicles (AGV) and autonomous mobile robots (AMR), which have soared in demand in recent years. For example, when a robot is in motion it can be difficult to push the emergency-stop switch and attempting to do so may place the worker at risk of being struck or trapped by the robot. Meanwhile, because of population decline, the growing shift toward automation, and other factors, the use of self driving vehicles and many other types of robots is likely to expand in the years ahead. We have responded to this safety challenge by developing an emergency-stop assist system that enables personnel to activate emergency stops from a safe position.
Our system is wireless switch worn on the arm of the worker in charge. By operating this switch, the worker can stop the AMR, AGV, or other robot in the same manner as pushing the emergency-stop switch installed on the robot. Since this system enables stops to be made from a safe position away from the robot, it helps to provide ANSHIN to operators.
A study of the system’s impact showed that it provides significant benefits, including with regard to hazard prevention, worker confidence, and emergency stopping performance.
Case2: ANSHIN Sensor
Recent years have seen a greater deployment of collaborative robots, which can operate alongside humans in diverse settings without the use of safety barriers. They are designed to stop moving upon contact, thereby eliminating the risk for serious collision injuries to humans. However, personnel may still feel uneasy about the risk of collision, even if minor. Also, the robots need to be restarted every time they automatically stop. Issues such as these can negatively affect productivity, efficiency, and worker well-being.
Our ANSHIN Sensor can temporarily stop robotic movement in response to proximity or even gentle contact, and can be applied to collaborative robots, AMR/AGV and other mobile systems, production lines where people and robots work together, and so forth. It thus can allay worker anxiety about machine contact and prevent the loss of productivity that comes from full shutdown of collaborative robots, other automated equipment, or production lines.
Case3: Trapping prevention system for aerial work platforms
A key principle of occupational safety management is to separate humans from machines by distance and time. However, this can be difficult to achieve at construction sites, as attested by the many cases of serious worker accidents due to contact with construction equipment. To help solve this issue, we have created a trapping prevention system that incorporates various sensors and an ergonomically designed three-position enabling switch we developed.
This system can be used on aerial work platforms to prevent personnel from becoming trapped against building structures such as ceilings and frames, thus protecting them from serious bodily injury. The greater safety and ANSHIN afforded to workers enhances their well-being.
Growth Strategy: Actions for advancing HMI-X 3
Ramp up our solutions for the growing material handling industry
Of the many different industries served by IDEC Group products, our current medium-term management plan is mainly focusing on four that have strong global growth potential: AGV/AMR, robotics, automotive, and machine tools. Notably, AGV/AMR are forecast to grow at an annual average of 20–30% in the coming years, pointing to significant growth potential for the material handling industry.
In January 2022, we entered into a partnership agreement with France-based ez-Wheel, a manufacturer that developed the world’s first safety wheel drive for AGV and AMR to incorporate drive control and safety features essential to safe automated driving. ISO (International Organization for Standardization)
publication of an international safety standard in 2020 prompted requirements for transportation robots and other mobile robots operating in areas with people to be equipped with a safe motion monitoring function, generating a growing need for products compliant with the standard.
Against this backdrop, demand has been rising for ez-Wheel’s lineup of safety wheel drives, which incorporate safety features necessary for complying with
standards. Recognizing this potential, we secured the exclusive marketing rights for ez-Wheel products in Japan through the partnership agreement, and since FY2023 we have offered diverse solutions integrating their products with our emergency-stop switches, safety laser scanners, and other safety devices.
The use of automated driving wheels is growing as distribution and manufacturing businesses increasingly consider adopting AMR to reduce staffing needs and workload through automated transportation. Meanwhile, our electric
power wheels, which make it easier for workers to transport heavy objects, have been the focus of many customer inquiries from the automotive industry, which deals with heavy items on a daily basis. We expect to see greater adoption of both types of wheels in the coming years.
In order to better respond to the different needs of diverse customers and industries, we are phasing in a system of support covering the four services below. As of FY2023, we have deployed services (1) and (2). Our ultimate goal is to provide full packaged solutions (including software) for building AGV
and AMR. We are exploring opportunities for partnering and M&A as an avenue for strengthening our software capabilities.
(1) Individual product sales
(2) Solutions packaging optimal products
(3) Packaged solutions customized for specific applications
(4) Full system setup
In addition, group company IDEC AUTO-ID SOLUTIONS CORPORATION offers a broad lineup of automatic identification devices that help to improve the efficiency of distribution operations. It is now expanding sales to serve the growing needs of the material handling industry.
The new medium term management plan’s minimum targets are sales of over 80 billion yen, operating income of over 13 billion yen, and an operating income margin of over 16% in FY2025, with the ultimate aim of realizing an operating income margin of 20% in the long term. We have also created a new slogan, “PASSION FOR YOUR SUCCESS” and will create an environment that enables us to realize customer success, by providing advanced products, solutions and exemplary services.
We are committed to helping customers overcome their challenges by creating new value for them. To do this, we are actively leveraging our technological strengths in core areas such as HMI, safety, and ANSHIN, while further reinforcing our software and IoT capabilities.
Improving profitability, enhancing business foundation and ESG initiatives
Building the foundation for high profitability
We are realigning our global network of manufacturing, sales, and distribution sites as part of our efforts to improve profitability, a major focus of our medium-term management plan. We took action to shrink fixed costs by consolidating our nationwide network of sales offices in Japan into two locations, one in Tokyo and one in Osaka, in FY2022—an action spurred by the COVID-19 pandemic—and by carrying out realignments and structural reforms at our overseas manufacturing/distribution sites and supply chains.
Moreover, we globally raised our product prices to reflect the increased costs of raw materials, and lowered our cost ratio by optimizing our selling prices and restructuring our product mix to increase the share of new products offering greater profitability. As a result, we raised our FY2023 gross profit margin to 44.6% and operating income margin to 16.8%, enabling us to reach two key targets of the medium-term management plan in its first year.
Our sales-related initiatives have included launching the Solution Business Promotion Department, recruiting and training talent from within and outside the Group to lead the expansion of our business in providing solutions for customer challenges, and strengthening our sales organization through the collaboration of related departments. For our component sales, we are leveraging our established sales networks to further grow sales, while at the same time stepping up the formation of new networks in each region that realign our distributor relationships to focus on distributors eager to sell IDEC products.
In FY2024, we will implement structural reforms to build the foundation for globally expanding our businesses and increasing earnings. In particular, we will pursue production reforms aimed at strengthening our global competitiveness. We will also separate our procurement and supply chain management functions into an independent organization to enable objectively optimized procurement, with the aim of lowering costs and building optimal supply chains across our Group. We are also working to radically overhaul our production systems and processes to achieve quality and cost improvements.
Enhancing operational efficiency through DX
We are seeking to strengthen our business foundation by accelerating DX initiatives across our Group that can realize greater operational efficiency and leaner management. The ERP and SCP systems that we are now introducing globally are interlinkable with various existing systems, and thus will enable integrated management of marketing, sales, order handling, production planning, procurement, inventory, and other functions. This project is starting with the head office and will be phased in globally with completion in FY2025, the final year of the current medium-term management plan.
At the same time, we are carrying out Group-wide work process reforms, as well as workstyle reforms—such as introduction of discretionary work and flextime systems while making effective use of existing systems—in an effort to realize flexible work arrangements and improve employee engagement.
Further strengthening our environmental initiatives while pursuing development of technologies and new products
We believe that taking actions toward sustainability, particularly measures for addressing climate change, is an integral part of fulfilling our social responsibilities as a global corporate group. Accordingly, we have defined “response to climate change” as our third material issue.
Also, we have set sustainability KPIs necessary for attaining our vision for 2030, and are implementing an action plan for achieving those targets.
[How we address climate change in our vision for 2030]
-Contribute to the reduction of the environmental impact of customers and society through our technologies and products.
-Reduce CO2 emissions, including by utilizing renewable energy at our sites.
In my role as Senior Executive Officer in charge of R&D & Environment, I constantly think about how we, as a manufacturer, can effectively balance both our pursuit of development and our response to environmental issues. This report’s section on natural capital presents our thinking and initiatives concerning environmental management, risk/opportunity analysis, transition opportunities, and the like.
I will strive to spread our Group’s awareness of environmental action as not only a risk-related factor with significant implications for our business continuation, but also an area of business opportunity with great potential
for us as a manufacturer.
Enhance ESG initiatives
Promote reduction of environmental impact to achieve carbon neutrality
IDEC has formulated a new vision for 2050 to “realize a safer and more sustainable world that brings happiness and ANSHIN to all people.” To achieve the objective, the medium-term management plan focuses on strengthening ESG activities, and it also promotes reducing environmental impact to attain the interim goal of accomplishing the sustainability KPIs related to climate change, with the goal of achieving carbon neutrality in 2050.
As part of these initiatives, we are promoting the effective use of limited resources, based on the concept of a “circular economy.” At the stage of designing and developing products, we are working to reduce the number of parts and product weight, a quantify use of recycled plastics, and so on. In addition, we phased the eco-friendly degree of new products based on our own standards. New products that meet those standards are certified as “enhanced eco-friendly products”, and our original eco-mark is stamped on them, compliant with ISO/JIS Q 14021 (Type II).
Moreover, in manufacturing and logistics processes as well, we are working to reduce environmental impact—such as by using bubble wrap with film containing 25% or more biomass plastics as product packaging materials—and are proceeding with management practices that emphasize environmental issues.
Since FY2023, we have introduced internal carbon pricing (ICP) as a framework to promote environmentally conscious investment. Converting CO2 reduction amounts into money promotes the use in investment decisions of the improved return on investment achieved through the adoption of ICP.
Increase investment in human capital, promote workstyle transformation and so on to increase engagement and strengthen the business foundation
In 2019, IDEC conducted its first employee engagement survey, and in 2022 conducted a second survey. Five issues from the results of the 2019 survey were selected, and we are currently promoting activities to resolve those issues. In the 2022 survey, the scores for the major metrics “Total Employer Attractiveness” and “Total Workplace Attractiveness” improved, and the scores for most of the other items improved as well.
IDEC also plans to tackle new issues indicated in the results of the 2022 survey. Increased investment in human capital and workstyle transformation are already included in the sustainability KPIs, so we plan to improve human resource development systems and promote workstyle transformation and so on to boost engagement further and strengthen the business foundation.